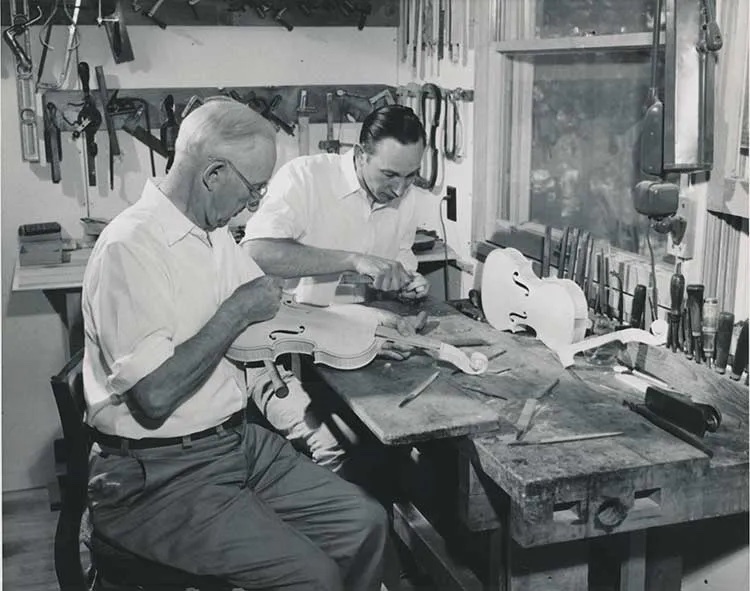
貝克製琴王朝在森林中汲取靈感(2023, String雜誌)
Nov 12. 2023
Carl G. and Carl F. Becker at the Pickerel bench in 1950. Courtesy of the Becker family
1950年,卡爾·G·貝克(Carl G. Becker)與卡爾·F·貝克(Carl F. Becker)在皮克瑞爾湖的小提琴製作工作台上工作。圖片由貝克家族提供。
Named “Fiddle Sticks,” the Becker's 14-acre Wisconsin compound was the birthplace of some of the most valuable American violins ever built.
名為「Fiddle Sticks」的貝克家族威斯康辛州佔地14英畝的莊園,是一些最具價值的美國小提琴的誕生地。
By Cliff Hall | From the November-December 2023 issue of Strings Magazine
作者:克利夫·霍爾(Cliff Hall) | 出自《Strings Magazine》2023年11月至12月刊
The Becker Violin Making Dynasty Found Its Inspiration in the Woods
Way up in the Northwoods of Wisconsin on the shores of Pickerel Lake is a small cadre of cabins on about 14 acres of bucolic land. Named “Fiddle Sticks,” this compact compound was the birthplace of some of the most valuable American violins ever built. But the output of those violins depended entirely upon how the fish ran.
“If the fish are biting good, the violin making may result in eight to ten or a dozen finished pieces. If the fish are few, we bring home to Chicago 15 to 18 violins.” These were the words of Carl G. Becker (1887–1975) in a 1954 interview with the Chicago Tribune. A decade earlier, he described this routine to Piano and Radio Magazine in more detail. “Well, I spend a pretty good day working, knock off about 3:30, then do a little trout fishing,” said Becker. “That’s my favorite recreation, and Pickerel Lake’s as good as they come for it.”
在威斯康星州北部森林的皮克瑞爾湖(Pickerel Lake)岸邊,有一片佔地約14英畝的田園土地,上面坐落著幾間小木屋。這個名為「Fiddle Sticks」的緊湊小村落,曾是一些最珍貴的美國小提琴誕生的地方。但這些小提琴的產量完全取決於魚群的活躍程度。
「如果魚咬得好,小提琴的製作可能會完成八到十把,甚至一打。要是魚少,我們就帶回芝加哥十五到十八把小提琴。」這是卡爾·G·貝克(Carl G. Becker,1887–1975)在1954年接受《芝加哥論壇報》(Chicago Tribune)採訪時的話。十年前,他在接受《鋼琴與收音機雜誌》(Piano and Radio Magazine)採訪時更詳細地描述了這個日常。「嗯,我一天大部分時間都在工作,下午三點半左右停工,然後去釣一些鱒魚,」貝克說。「那是我最喜歡的休閒活動,而皮克瑞爾湖是最棒的釣魚地之一。」
Though seemingly unimportant in the Becker family’s violin making legacy, the calm and peace of this lake were actually essential to it. Though Carl G. and his son, Carl F. Becker (1919–2013), spent most of their time at the repair benches of William Lewis and Son in Chicago, a leading Chicago violin dealer, from the first of May until September, the two left the instrument restoration world behind to rejuvenate their own creative spirits in the seclusion of the Wisconsin wilderness.
“Repair gives the opportunity to meet with many musicians and help them with their musical journey… but making requires a different mindset,” says Carl F.’s daughter (who is also a luthier) Jennifer Becker. “You have to be in a quiet state of mind, focused but relaxed. Turmoil around you does not work to create something beautiful; interruptions make it very hard to keep the work flowing, so you really have to focus when you are making in order to achieve any progress.”
Carl F.’s son Paul also recognizes why this separation was necessary. “Repair work and restoration work are always at odds with making. If you do more restoration work, you make fewer instruments. Sometimes it is an economic decision, such as during a depression or the pandemic. These are times you just can’t make violins,” says Paul.
雖然看似與貝克家族的小提琴製作傳承無關,但這片湖泊的寧靜與安詳其實對此至關重要。雖然卡爾·G(Carl G. Becker)和他的兒子卡爾·F(Carl F. Becker,1919–2013)大部分時間都在芝加哥知名小提琴經銷商威廉·路易斯與兒子公司(William Lewis and Son)的修復工作台前度過,但從五月初到九月,他們都會遠離樂器修復的世界,在威斯康星的荒野中隱居,以恢復自己的創作靈感。
「修復的過程提供了與許多音樂家交流的機會,並幫助他們完成音樂旅程……但製作需要完全不同的心態,」卡爾·F的女兒珍妮弗·貝克(Jennifer Becker,亦是一名製琴師)說道。「你必須處於一種安靜的心境,專注但放鬆。周圍的混亂無助於創造美好的事物;中斷會讓工作難以順利進行。因此,當你製作時,真的需要全神貫注,才能取得進展。」
卡爾·F的兒子保羅(Paul)同樣認識到這種分離的重要性。「修復工作和製作工作之間始終存在矛盾。如果你做更多的修復工作,製作樂器的機會就會減少。有時這是一種經濟上的選擇,例如在經濟大蕭條或疫情期間。在那些時候,你根本無法專心製作小提琴,」保羅說道。
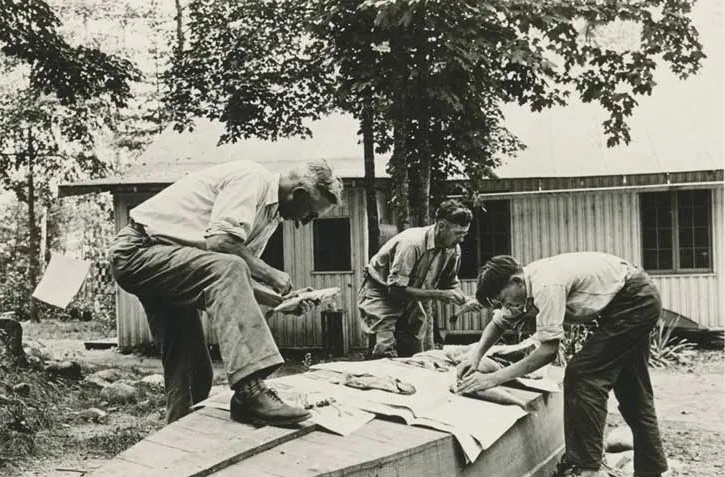
Trout fishing was one of Carl G. Becker’s (1887–1975) favorite recreations. Courtesy of the Becker Family
The Becker family musical journey started in 1864 in Chicago with the work of upholsterer/violinist turned luthier Herman Macklett (1834–84). In his book Known Violin Makers, John Fairfield called Macklett “a pioneer American violin maker of outstanding ability.” His daughter Adeline married Carl J. Becker (1858–1921), a German-born violinist who was a pupil of Joseph Joachim, and they had a son they named Carl G. Becker. Known as much for his instruction as his playing, Carl J. taught his son Carl G. Becker how to play the violin, but it was during one of their trips to see his luthier, William Lane, that Carl G.’s passion for instrument making was sparked.
“My grandfather was immersed in music, and he played the cello himself. He did talk to me when I was younger about walking Wabash Avenue and looking at all the fine instruments in the windows of the music stores, and he fell in love with violins. He started working at age 14,” says Paul. “This is the true beginning of the Becker line of instruments.”
Carl G. worked with John Hornsteiner until 1924, when one of Chicago’s biggest firms came knocking. “He accepted an invitation from William Lewis & Son to become master luthier and instrument appraiser, with the understanding that they would allow him to spend summers up in northern Wisconsin to make instruments,” writes Paul Becker on his website. “And to fish.”
The work on his bench at Lewis & Son did not go unnoticed..
貝克家族的音樂旅程始於1864年的芝加哥,源於一位由裝潢師兼小提琴家轉職為製琴師的赫爾曼·麥克萊特(Herman Macklett,1834–1884)。在約翰·費爾菲爾德(John Fairfield)所著的《知名小提琴製作者》(Known Violin Makers)一書中,麥克萊特被稱為「具有傑出能力的美國小提琴製作先驅」。他的女兒阿德琳(Adeline)嫁給了卡爾·J·貝克(Carl J. Becker,1858–1921),一位出生於德國的小提琴家,也是約瑟夫·約阿希姆(Joseph Joachim)的學生。他們有一個兒子,取名為卡爾·G·貝克(Carl G. Becker)。
卡爾·J以他的教學和演奏而聞名。他教導兒子卡爾·G如何拉小提琴,但真正點燃卡爾·G對製作樂器的熱情,則是在他們一次拜訪製琴師威廉·雷恩(William Lane)的旅途中。
「我的祖父沉浸於音樂世界,他自己也拉大提琴。他曾在我年輕時跟我聊過,說他走在瓦巴什大道(Wabash Avenue)上,看著音樂商店櫥窗裡的精美樂器,便愛上了小提琴。他14歲時便開始工作了,」保羅說。「這才是貝克製琴世家的真正起點。」
卡爾·G曾與約翰·霍恩施泰納(John Hornsteiner)共事,直到1924年,芝加哥的一家大型公司找上門來。「他接受了威廉·路易斯與兒子公司(William Lewis & Son)的邀請,成為該公司的首席製琴師及樂器鑑定師,條件是公司允許他每年夏天去威斯康星北部製作樂器,」保羅·貝克在自己網站上寫道,「順便釣魚。」
他在威廉·路易斯與兒子公司工作台上的作品並未被忽視……
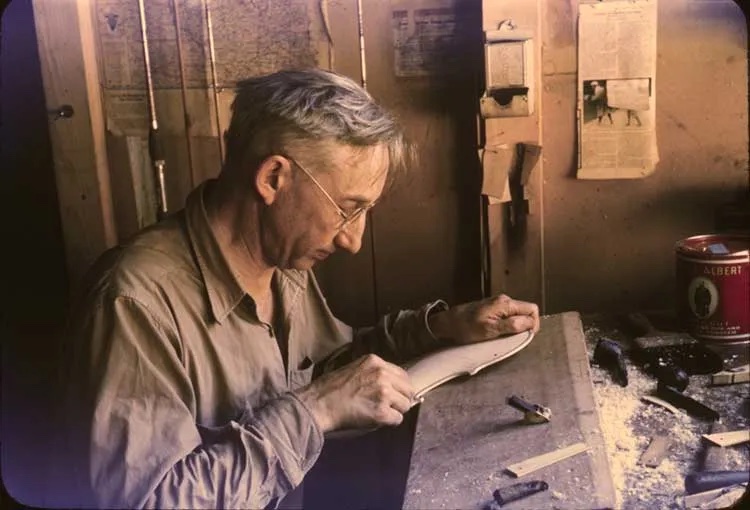
Carl G. Becker at the Fiddlesticks bench. Courtesy of the Becker Family
“Having the ambition common to all novitiates, [Becker] produced [his] first instrument in 1904 and accomplished a pronounced cleverness in conception as well as a thorough mastery of manipulation… Every detail is perfectly synchronized,” praised William Henley in his 1959 book Universal Dictionary of Violin & Bow Makers, “thus foreshadowing a fame which has since become universal in America.”
Though he garnered a strong reputation as an expert repairer and restorer, it was the soft varnish of his own making that the family built its name on. “Soft varnish is the only way to produce the high-quality tone that Beckers are known for. The care it takes to not scratch the varnish is worth the difference in tone. Soft varnish will naturally wear off with use so yearly checkups and polishing are recommended,” says Jennifer. “Soft varnish also takes a long time to dry, so it slows down the process of making. Long term, an extra few months is worth the wait.”
But the best was yet to come.
In 1937, shortly after graduating from high school, Carl G.’s son, Carl F., embarked on an apprenticeship journey with William Lewis & Son. Under his father’s watchful eye, Carl dedicated himself to the art of restoration, swiftly earning his own impeccable reputation in the field. One of his most prestigious assignments was the meticulous restoration of the renowned “Lady Blunt,” a 1721 Stradivari violin cherished by numerous musicians as one of the world’s finest.
“This man is the greatest repairman and maker of violins who ever lived. I may have been all right in my day, but I never had the patience to spend the time that he does. I did my work well, but I did it fast,” Carl G. told the Chicago Tribune toward the end of his life.
“Alongside him, I’m a butcher.”
This family affair continued its path when Jennifer became curious. “I have always wanted to make things, but I got a taste for carving when I was eight. My dad gave me a knife and gouge, and I used them to carve birds and fish. When I was ten, I announced my plans to make a violin. My dad was so surprised—out popped ‘No! You’re too young, and you’re a girl!’” says Jennifer. “So I made one out of scraps from their garbage box. My grandfather was impressed and said, ‘So what if she’s a girl?’ and encouraged me to try my hand at making.”
In addition to crafting instruments, Jennifer has played cello since her youth and continues to play in a community orchestra. “I started playing the cello the same year I started making,” she says. “My dad and grandfather both played instruments too. It does help to understand what you’re making.”
「懷著所有新手共有的雄心壯志,[貝克]在1904年製作了他的第一把樂器,展現出卓越的構思能力和精湛的操作技藝……每一個細節都完美協調,」威廉·亨利(William Henley)在其1959年的著作《小提琴與弓製作者通用詞典》(Universal Dictionary of Violin & Bow Makers)中讚譽道,「這預示了他在美國聲名鵲起,並最終成為家喻戶曉的製琴師。」
雖然卡爾·G·貝克以修復和修繕樂器的專業能力聞名,但真正讓家族成名的,則是他自製的柔性漆。「柔性漆是製造貝克家小提琴特有高品質音色的唯一途徑。雖然這種漆容易被刮傷,但音色上的差異讓這樣的細心呵護非常值得。柔性漆會隨著使用而自然磨損,因此我們建議每年進行檢查和拋光,」珍妮弗說。「柔性漆還需要很長的時間才能完全乾燥,這會延緩製作過程。但從長遠看,多等幾個月是值得的。」
但更精彩的故事還在後頭。
1937年,高中畢業後不久,卡爾·G的兒子卡爾·F開始了在威廉·路易斯與兒子公司的學徒之旅。在父親的悉心指導下,卡爾·F全身心投入修復藝術,不久便在這個領域樹立了自己的卓越聲譽。他的一項最負盛名的工作,是對「布朗特夫人」(Lady Blunt)小提琴的精細修復。這把1721年製的斯特拉迪瓦里小提琴被無數音樂家視為世界上最出色的小提琴之一。
「這個人是有史以來最偉大的小提琴修復師和製琴師。我也許在我的時代還算不錯,但我從來沒有像他一樣有耐心花那麼多時間。我做得很好,但我做得很快,」卡爾·G在生命的最後階段接受《芝加哥論壇報》採訪時說。
「與他相比,我就是個屠夫。」
這段家族傳承延續到珍妮弗身上時,開啟了新的篇章。「我一直都喜歡製作東西,但真正愛上雕刻是在八歲那年。我爸爸給了我一把小刀和一個凹刻工具,我用它們雕刻鳥和魚。十歲時,我宣布自己打算製作一把小提琴。我爸大吃一驚,脫口而出:『不行!妳太小了,而且妳是個女孩!』」珍妮弗回憶道。「於是我用他們垃圾箱裡的廢料做了一把。我爺爺看到後非常驚訝,說:『她是女孩又怎麼樣?』並鼓勵我繼續嘗試。」
除了製作樂器,珍妮弗從小就開始拉大提琴,至今仍在社區管弦樂團中演奏。「我開始拉大提琴的那一年,也是我開始製作樂器的時候,」她說。「我的爸爸和爺爺也都會拉樂器。了解樂器的演奏方式,確實有助於製作它們。」
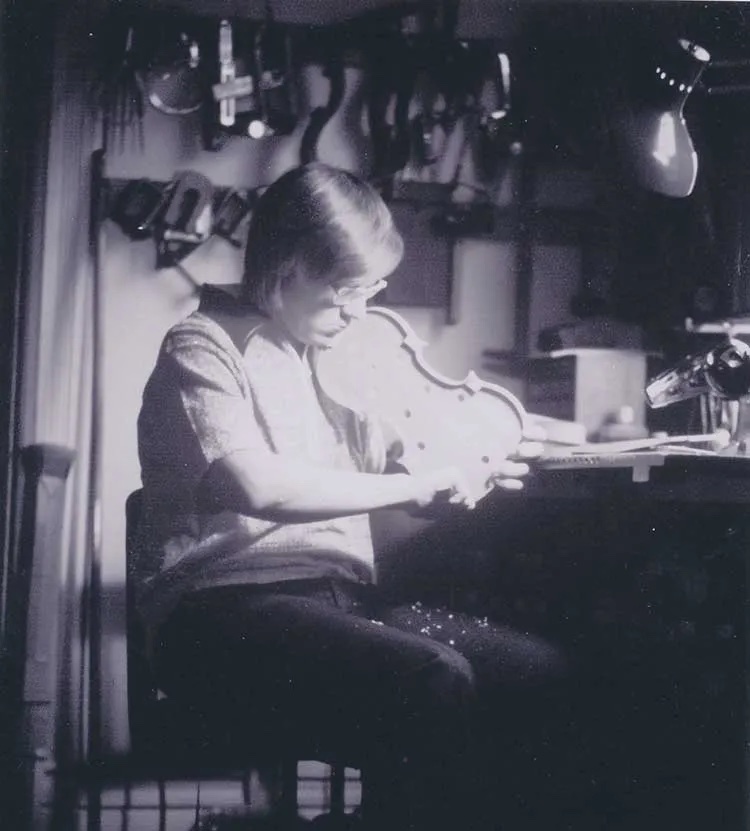
Paul C. Becker with his first violin on form. Courtesy of the Becker Family.
At the age of 14, Paul C. Becker joined his father and grandfather in the craft. Collaborating with his grandfather, Paul successfully built his inaugural violin. “It was during summers at Pickerel that I learned how to make a violin. I was first taught to make my own form and make a violin from scratch, by hand, without using any power tools. While I watched dad use power tools to rough out instruments, I have to admit I was fascinated with that process,” says Paul. “Dad would say it doesn’t matter what takes the wood out, it’s the result that does.”
For a short period, Paul ventured beyond Carl Becker and Son, Ltd., initiating his own woodworking enterprise, which specialized in crafting bespoke furniture. However, he ultimately realized that his true passion lay in the art of violin making, and he has since gained the trust of violinists worldwide.
“Many people don’t realize that there are different things that luthiers do—making violins, restoring violins, and tonal adjustments—and a luthier who’s wonderful in one area might not be who you want to see for another. Paul’s father was legendary at being able to slightly tweak the bridge and soundpost and make a good violin sound even better, and he taught Paul all his secrets. I’ve trusted Paul with my 1742 ‘ex-Bazzini, ex-Soldat’ Guarneri del Gesù for more than 20 years,” says violinist Rachel Barton Pine. “My concert touring constantly brings me from one climate to another. For example, this summer I was in the low humidity of Santa Fe, New Mexico, and then in the high humidity of Brazil shortly thereafter. This causes the violin’s wood to expand and contract, and its voice can suffer. Paul always knows how to bring things back to perfect condition, and I couldn’t be more grateful for his incredible skills!”
14歲時,保羅·C·貝克(Paul C. Becker)加入了父親和祖父的行列,學習製琴技藝。在祖父的指導下,保羅成功完成了他的第一把小提琴。「在皮克瑞爾湖的夏天,我學會了如何製作小提琴。我首先學會了如何製作自己的模具,並從零開始,完全手工製作小提琴,不使用任何電動工具。雖然我看到爸爸使用電動工具來粗加工樂器時,對這個過程感到著迷,」保羅說。「爸爸常說,取出木材的方法不重要,重要的是結果。」
短暫的一段時間裡,保羅曾離開家族企業「Carl Becker and Son, Ltd.」,創立了自己的木工公司,專門定製家具。然而,他最終意識到自己真正的熱情還是在製作小提琴的藝術上,並因此贏得了世界各地小提琴家的信任。
「很多人不知道製琴師的工作內容有多種——製作小提琴、修復小提琴以及調整音色。而一位在某個領域出色的製琴師,可能並不適合其他領域的工作。保羅的父親在微調琴橋和音柱方面堪稱傳奇,他能讓一把優秀的小提琴變得更加出色,並且把這些秘訣都傳授給了保羅。我已經把我的1742年『前巴齊尼,前索爾達』(ex-Bazzini, ex-Soldat)瓜奈里·德爾·傑蘇(Guarneri del Gesù)交給保羅維護超過20年了,」小提琴家瑞秋·巴頓·派恩(Rachel Barton Pine)說。「我的巡演經常讓我穿梭於不同的氣候。例如,今年夏天我去了新墨西哥州聖塔菲的低濕環境,之後又到了濕度很高的巴西。這些氣候變化會讓小提琴的木材膨脹或收縮,影響音色。但保羅總是知道如何讓小提琴回到最佳狀態,我非常感激他的卓越技藝!」
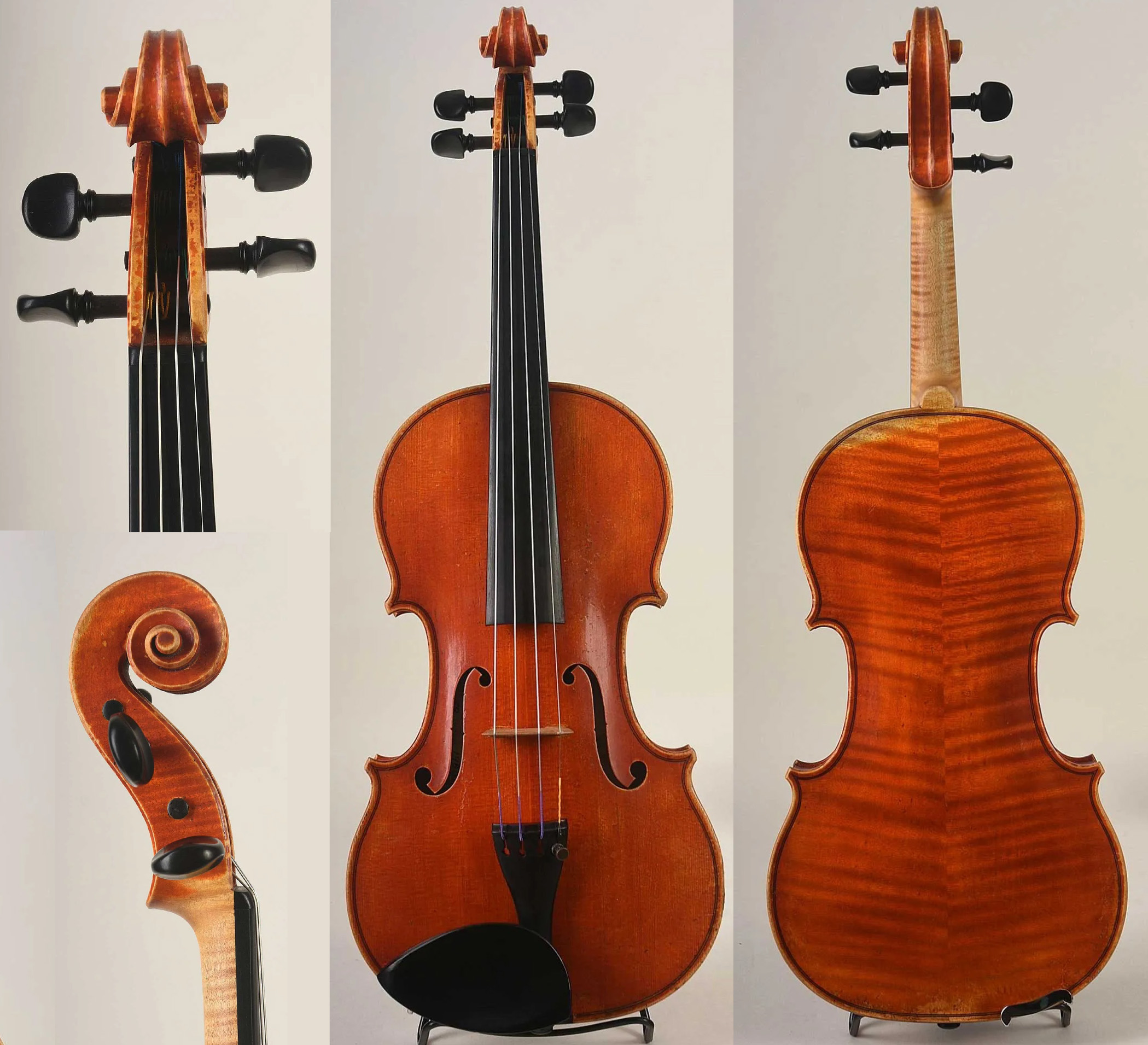
Becker violin, Courtesy of Fred Oster-Vintage Instruments
One change Paul has initiated is the use of modern woodworking machinery, though he is not the first Becker to employ this approach. “I incorporate as much machinery as I can, but nothing is entirely finished by machine, and you still have to be able to feel your work in order for it to express your passion. There are many violin makers that incorporate the use of a CNC in their work and many that don’t. I use a CNC for roughing [but] not finishing,” says Paul. “My grandfather used a duplicating machine to rough out tops and backs. My father used patterns and machines to rough out instruments. They all required finishing by hand.”
Carl F. Becker fulfilled his father’s wish to work as long as Antonio Stradivari did, as he continued to make instruments until his death in 2013 at the age of 93. Although he was unable to finish them all, this happenstance has afforded a unique opportunity for the family.
保羅引入了一些現代木工機械,雖然這並不是貝克家族首創的做法。「我儘量使用機械,但沒有任何一部分是完全由機器完成的。你仍然需要用心去感受你的作品,這樣它才能傳遞你的熱情。許多製琴師在工作中會使用CNC(數控機床),也有許多不會。我用CNC來進行粗加工,但不會用於最終完成,」保羅說。「我的祖父使用複製機來粗加工面板和背板。我的父親使用模板和機器來粗加工樂器。他們所有的作品都需要手工完成最後的細節。」
卡爾·F·貝克實現了父親希望他像安東尼奧·斯特拉迪瓦里(Antonio Stradivari)一樣工作到晚年的願望,他一直製作樂器直到2013年以93歲高齡辭世。雖然他未能完成所有的作品,但這為家族提供了一個獨特的機會。
Jennifer Becker. Courtesy of the Becker Family.
“I am currently finishing a cello with Jenny that was started by my father, myself, and Jenny,” says Paul. “It is unique to have all three of our hands involved. The three of us are also collaborating on two violas. Dad did most of the work of designing and making a viola that would produce a great sound. And so we also have these two instruments we all worked on, which fills me with pride, because they’re really quite perfect.”
Upon his passing, the family also inherited a collection of fractional-size instruments that had been completely redone by apprentices to provide the best quality sound for students. They inspired the emergence of a new branch of the family business.
“The family started the Becker Family Foundation in November 2018 to encourage students in their pursuit of a stringed-instrument education. This original collection was and is continuing to be used by small ensembles in the Southeast,” says Paul and Jennifer’s sister (and Carl F.’s daughter) Marilyn Becker, founding member and treasurer of the foundation. “Our purpose is to help remove those barriers preventing our young students’ earnest development. The foundation cannot do everything for the student, but we can help.”
Pine has seen the impact the foundation has made as well. “It’s very exciting that Paul and his siblings are now running their own Becker Family Foundation, which is making an important difference in the lives of many deserving young musicians,” she says.
While so much has changed in the nearly 120 years that the Becker family has been making violins in the United States, one constant that has remained is Fiddle Sticks. Though the rural enclave is no longer a place for making instruments (as Paul is based in Chicago and Jennifer in Saint Paul), they continue to use it as a family retreat.
“My children and my grandchild still go up there to fish during the summer. I personally like to spend my time up at the cabin chopping wood and building fires,” says Jennifer. “Being in the forest, surrounded by wood in its rawest form, is an incredibly healing, peaceful, and inspiring experience for me.”
我目前正在和珍妮一起完成一把大提琴,這把琴是由我父親、我和珍妮共同開始製作的,」保羅說。「能夠同時融入我們三個人的手工,是一件非常特別的事情。我們三人還在合作製作兩把中提琴。父親為設計和製作一把音色優美的中提琴做了大部分的工作。因此,我們也有了這兩件由我們共同完成的作品,這讓我感到非常自豪,因為它們真的非常完美。」
在卡爾·F.·貝克去世後,家族還繼承了一批經由學徒完全重製的小尺寸樂器,這些樂器專為學生提供最佳音質而設計。這批樂器激發了家族業務的新分支。
「2018年11月,家族創立了貝克家族基金會,旨在鼓勵學生追求弦樂器教育。這批原始樂器已經並將繼續被東南部地區的小型合奏團使用,」珍妮和保羅的妹妹瑪麗蓮·貝克(Marilyn Becker)說道。她是基金會的創始成員之一,同時擔任財務主管。「我們的目的是幫助那些因障礙無法全力發展的年輕學生。雖然基金會無法為學生提供一切,但我們可以提供一些幫助。」
小提琴家瑞秋·巴頓·派恩也見證了基金會的影響力。「能看到保羅和他的兄弟姐妹們現在運營著自己的貝克家族基金會,並對許多值得幫助的年輕音樂家的生活產生重要影響,這真的很令人興奮,」她說。
雖然貝克家族在美國製作小提琴的近120年裡經歷了許多變遷,但有一件事始終未變,那就是「Fiddle Sticks」。雖然這個鄉間避世地現在不再用來製作樂器(因為保羅的工作室位於芝加哥,而珍妮的工作室在聖保羅),它依然是家族的休閒之地。
「我的孩子和孫子現在夏天仍會到那裡釣魚。我自己喜歡在小木屋裡劈柴、生火,」珍妮說。「置身於森林之中,周圍都是最原始形態的木材,對我來說是一種極具療癒力、平和且充滿啟發的體驗。」